This tutorial teaches you how to run a simulation interactively and what must be done in order to drill.
Create a New Simulation
A new simulation can be created from the configuration view or from the simulations view by pushing the “New Simulation” button.
When creating a new simulation, you need to specify the name of your simulation and/or any advanced settings you would like. In the “Initial conditions” tab you can set initial bit, initial top of string position, and initial pit condition.
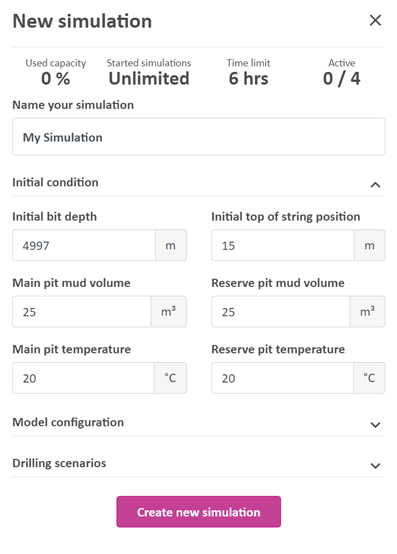
In the “Model configuration” tab, various models can be turned on or off. You can choose between a steady-state and transient torque and drag model. The steady state torque and drag model is a simplified torque and drag model. Simulation step duration can be set to between 0.1 and 1 second. Note that decreasing the step duration will decrease the simulation speed. The transient torque and drag model is an advanced torque and drag model. The step duration is 0.1 second, however the actual step in the torque and drag model is 10 ms. Note that it takes a longer time to simulate with this model than the steady state torque and drag model. For the transient torque and drag model you can choose between the MSE and Detournay ROP model.
It is also possible to turn off the temperature mode. By default, the temperature model in the drillstring and annulus is equal to the geothermal temperature, but it is also possible to start from a predefined temperature profile specified in the configuration page. In addition, a transient cuttings model and a gel model can be turned on.
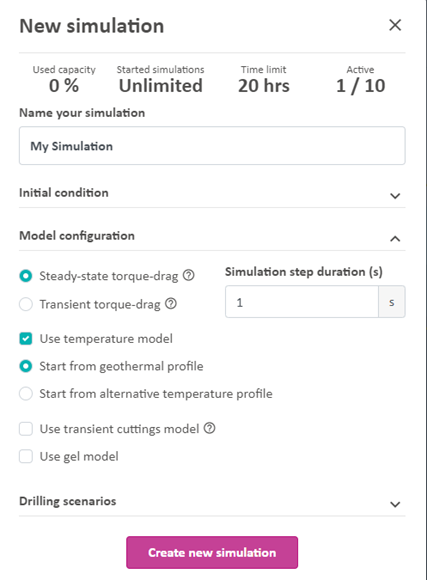
In the “Drilling scenarios” tab, you can select whether you want to be able to simulate influx/losses or not. Influx and losses are by default turned off. No influx and losses will then occur in the simulation even if the pressure in the open hole section is below the pore pressure or above the fracture pressure. If you choose “Based on geopressure”, the geopressure curves will define your boundaries for influx and losses, but no Influx or loss will occur before the kick-off time, which will give the user a chance to start circulation or in other ways preparing the simulation of the influx or loss. Influx will occur if the pressure in the open hole section is below the pore pressure and losses will occur if the pressure in the open hole section is above the fracture pressure. The intensity of the influx or loss is a function of the formation properties such as permeability and porosity that can be edited in the Geology configuration editor.
Direct influx/loss will override the geopressure settings. At the kick-off time, an influx/loss will occur at the specified depth (MD) with the specified mass rate. The influx/loss will stop when the accumulated influx/loss reaches the specified total mass. The direct influx/loss cannot occur in the riser.
To simulate pipe washout, the “Use pipe washout” checkbox must be selected when initializing the simulation. The location of the washout is determined by a distance from the bit. The washout must be located below the bop and above the bit.
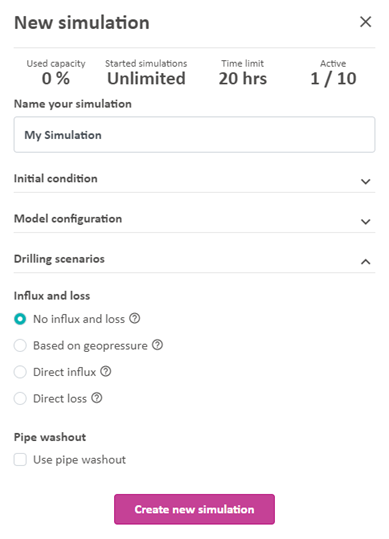
Click the “Create new simulation” button to create a simulation. When creating a simulation, the computer model is first initialized and then (after a few seconds) it is ready to calculate the dynamic state of the well based on your choice of drilling parameters (setpoints).
Drilling Parameters (Setpoints)
In the current version you can control the following parameters:
- Main pump flow rate
- Hook speed
- ROP
- Surface RPM
- MPD Choke Opening
- MPD pump flow rate
- Density at inlet
- Pumped fluid
- BOP Choke Opening
These drilling parameters are setpoints, which means that they represent the desired or target value for the respective simulated process value. Both in OpenLab and in real life, there is a time-delay before the difference between the setpoint and process value is minimized, which is dependent on the characteristics of the component. To adjust the characteristics of a component, please see the Rig configuration editor.
Beware that the density of the fluid into the well (Density in) is typically not a drilling parameter which is possible to change “on the fly” in a real drilling operation. With today’s equipment, you need to change the density by adjusting the content of weight material in the drilling fluid on the rig, which takes some time. However, in OpenLab we allow the users to change inlet density on the fly because it allows use of this parameter as a manipulated variable in process control simulations. The density given in the Fluid editor will still be your default density for this particular fluid, and the fluid that remains in the pit tank will have the default density. When you start a simulation, your well will always be filled with the fluid named as Fluid 1 in your Fluid editor. The “Density in” only allows you to change the density of the fluid that is being pumped into the well.
Manual Mode
In Manual mode you are free to change any of the setpoints during the simulation. In the current version of the simulator, we have set the length of a simulation step to one second. If you chose to run a simulation in “real time”, the simulation performs one step per second. You can also run the simulator faster than real time, in the fast-forward mode. In fast forward, the speed of the simulation will depend on your computer device, internet connection, and number of simulation graphs.
A typical simulation speed is around 10x, which means 10 times faster than real time. In Manual mode each drilling parameter can be changed at any time, but be aware that in fast forward there might be some time-delay from when you enter a value until it is used in the simulations, since the simulator is running a few steps ahead of what is visible to you in the browser. If you want to simulate only one step ahead, you can do so by pushing the “Run a single step” button . When pausing a simulation, the simulation is temporarily put on hold and can be resumed at any time. If you do not resume a simulation within a certain time, or if you log out, the simulation is automatically stopped and completed by the system. This is to avoid too many ongoing simulations in the OpenLab system. If you push “Stop and complete a simulation”, the simulation is saved and cannot be resumed. After a simulation has been completed, you can export the setpoints by clicking the “View setpoints” and then Export.
If you want to run through a pre-defined set of drilling parameters, you may use the Sequence mode. This will also result in a higher simulation speed.
Start Drilling
In order to drill and advance the open hole, there are several parameters that must be set. These are:
- Flow Rate
- Hook speed (positive is downward)
- Desired ROP (how fast you wish to drill)
- Surface RPM
Once you click play and these parameters are set, you will begin to drill after touching bottom.